Het is moeilijk voor te stellen, maar er zijn situaties op bouwplaatsen die onze meetapparatuur tot het uiterste drijven. Aanvallen van graafmachines, gemorst zand, zwemlessen of brand zijn een aantal voorbeelden hiervan.
Om onze meetapparatuur zo goed mogelijk voor te bereiden op deze vormen van alledaagse stress, doen we herhaaldelijk tests en inspecties in Haselünne.
Hier zijn een paar voorbeelden uit dagelijks leven op de bouwplaats en geven we inzicht in de interne processen bij Esders.
Waarschuwing: de volgende beelden kunnen als schokkend worden ervaren. 😉
OLLI
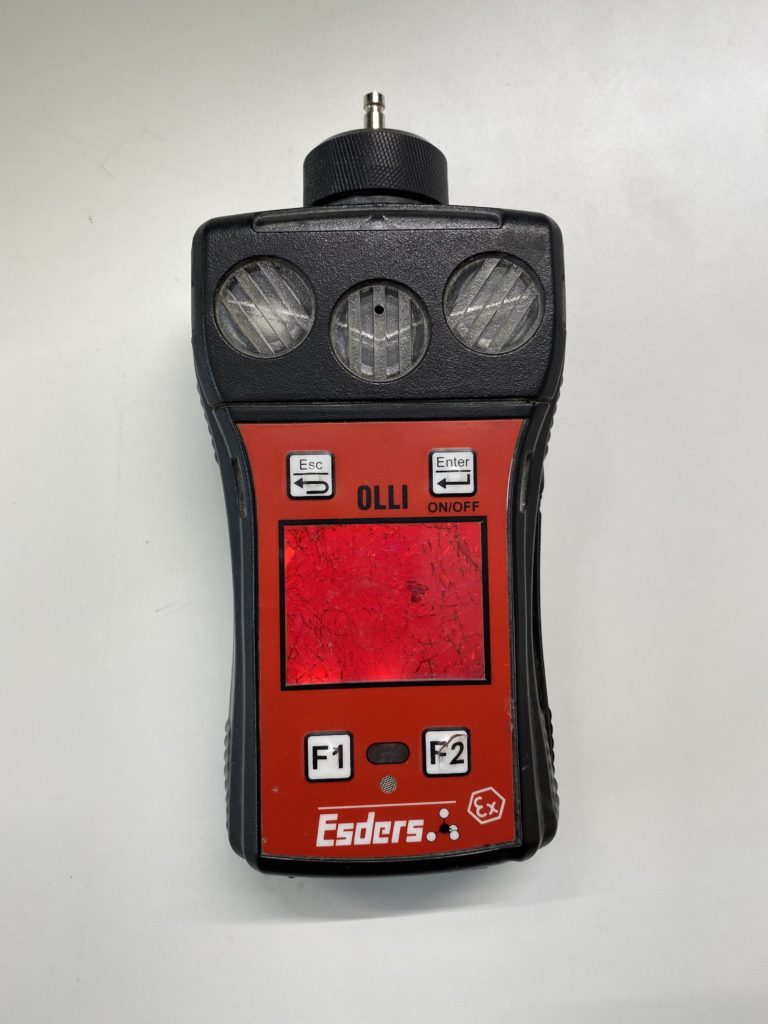
Onze prachtige OLLI werd op relatief zachte grond overreden door een graafmachine. U kunt hem nog aanzetten en het alarm zal nog werken, maar veilig werken met dit meetapparaat is zeker niet meer mogelijk omdat de behuizing scheurtjes heeft. Ook het display functioneert niet meer.
DruckTest GaWa
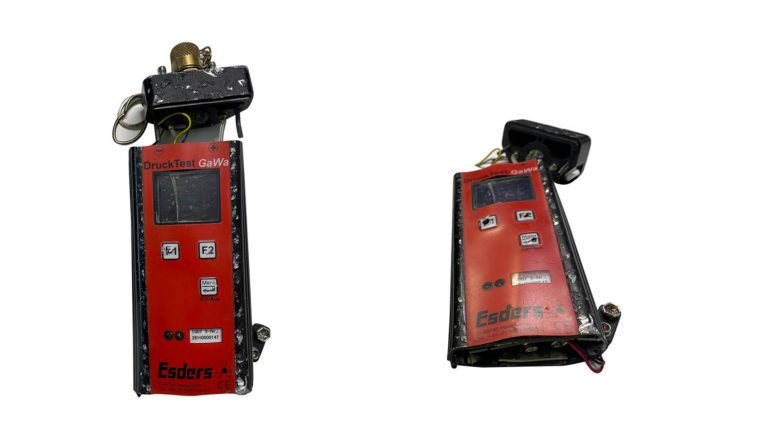
Verder presenteren we de DruckTest GaWa “platte versie / slimline”. Ook hier was een graafmachine in het spel. De aluminium behuizing is verbogen, maar de ingebouwde sensor is nog in goede staat doordat de sensorhouder massief gefreesd is.
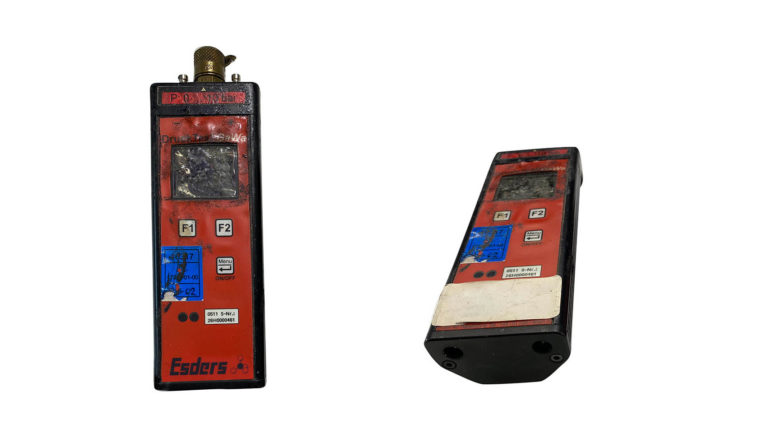
Naast de graafmachine is ook open vuur een natuurlijke vijand van onze meetapparatuur. De Drucktest GaWa die hier wordt getoond, lag in een auto die is uitgebrand. Niemand weet wat er is gebeurd. Wij verzoeken u om rekening te houden met het temperatuurbereik van de apparaten.😂
DruckTest memo
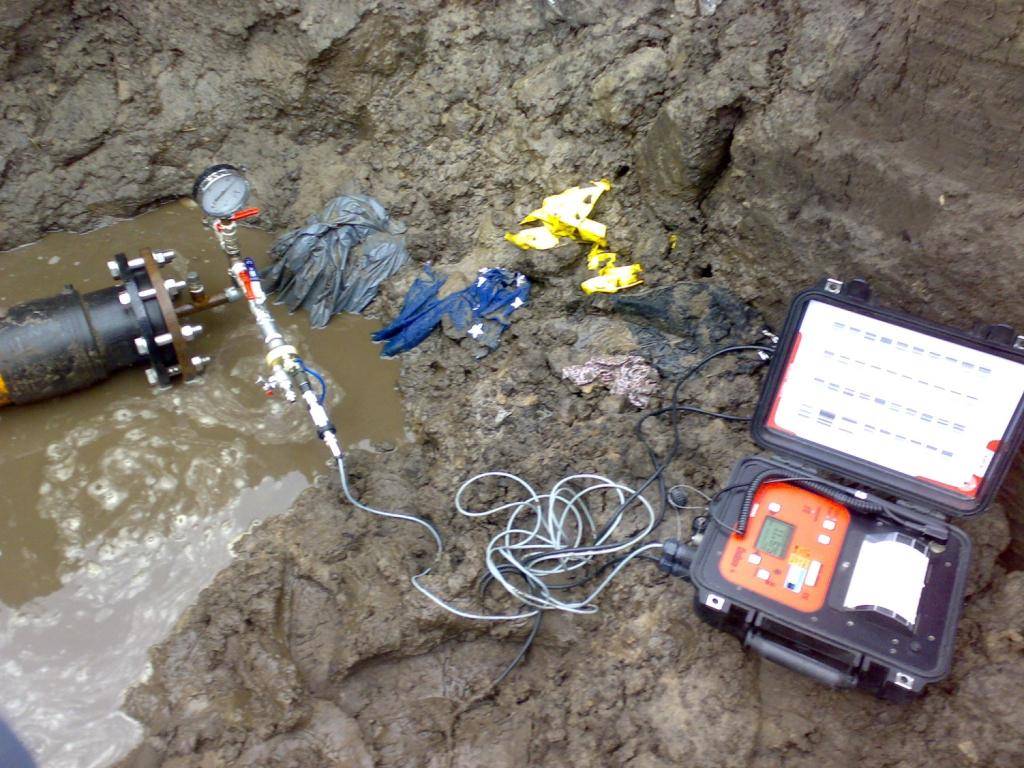
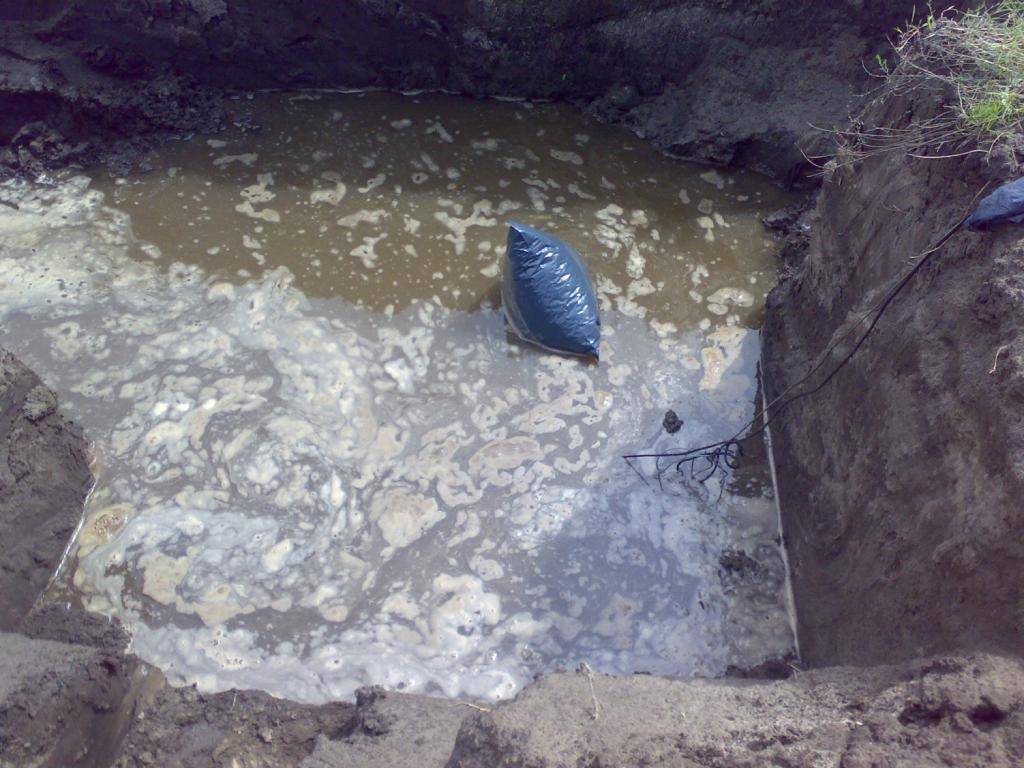
Opgravingen die niet goed beveiligd zijn, stellen soms de hoogste eisen aan ons materieel. Deze Drucktest memo heeft de zwemles (inclusief duiken) succesvol doorstaan.
Tests voor de harde praktijk – don’t try this at home!
Wij voeren zelf ook graag testen uit in Haselünne, zoals met deze OLLI in ontwikkeling, die uit het raam valt. We hebben vastgesteld dat de bevestiging van de printplaat nog niet optimaal is.
Heel elegant in de vliegfase, maar behuizing en sensoren hebben veel last van de impact bij de landing.
Deze interne experimenten waren voor ons in 2019 echter niet meer voldoende en we hebben een hooggekwalificeerd team van experts samengesteld. Onze experts hebben in het laboratorium verschillende experimenten uitgevoerd onder extreme omstandigheden.
Mocht u het nog niet gezien hebben, hier zijn de opnames van ons testlaboratorium.
Alle gekheid op een stokje - hoe we onze producten echt testen bij Esders
Voor nieuwe producten is er een nauwkeurig voorgeschreven proces van ontwikkeling tot levering en daarna.
Nieuwe producteisen komen veelal voort uit marketing, sales of management en worden verzameld door productmanagement en vervolgens in detail besproken met de ontwikkelingsafdeling.
In de volgende stap worden de eerste technische documenten gemaakt en prototypes ontwikkeld. Hierbij is een ATEX-expert betrokken als hardware ontwikkelaar. Niet al onze producten behoeven certificering op het gebied van explosiebeveiliging.
Handling is erg belangrijk voor de behuizing. Waar we vroeger probeerden om nieuwe behuizingen te bouwen met houten modellen of zelfs Lego, kan een 3D-printer nu helpen om de bediening te testen en indien nodig optimalisaties uit te voeren.
OLLI prototype
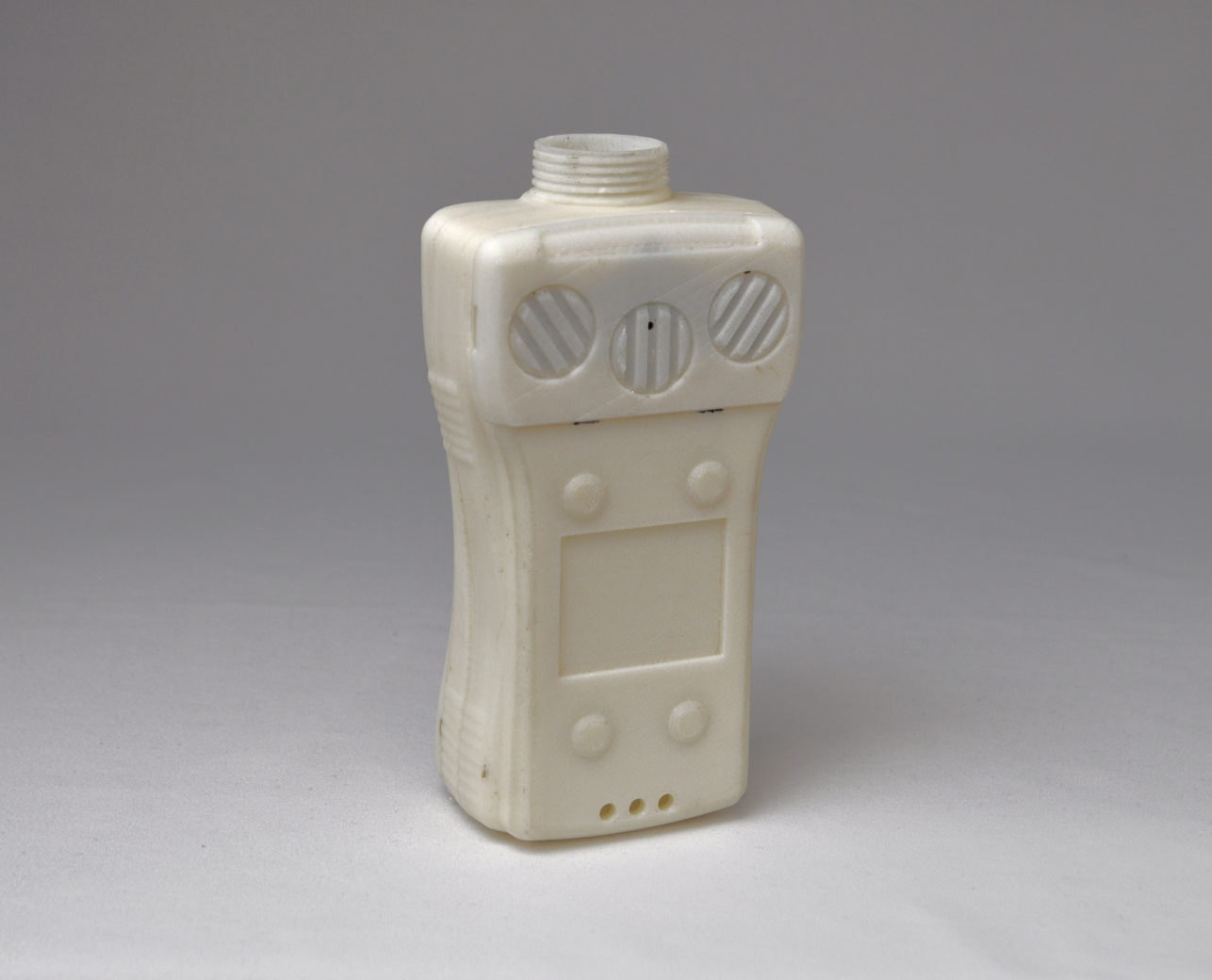
De eerste prototypes worden gebouwd en getest. Hierbij zijn kwaliteitsborging (QA) en ontwikkeling betrokken. Moeten er in een apparaat nieuwe sensoren worden geïnstalleerd, die nog niet eerder door ons zijn gebruikt, dan worden deze voor gebruik getest onder verschillende omgevingsomstandigheden (temperatuur, vochtigheid, luchtdruk, gasconcentraties).
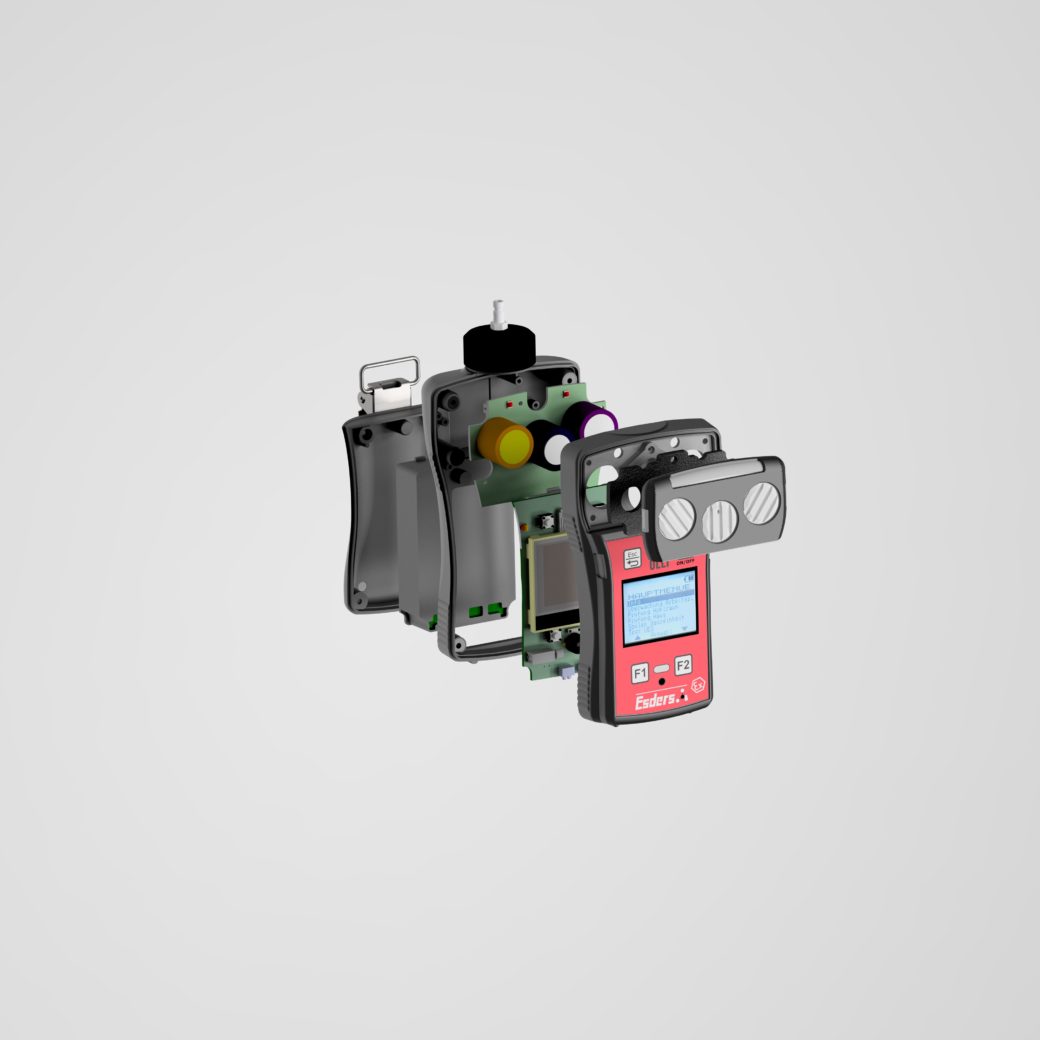
Functietesten en geschiktheid voor bouwplaatsen
We voeren een algemene functietest uit en diverse functietesten bij verschillende temperaturen in onze klimaatkast.
Vervolgens wordt de meetnauwkeurigheid gecontroleerd onder verschillende omgevingsomstandigheden (hoge & lage temperaturen, verschillende luchtvochtigheid, verschillende omgevingsdruk in de klimaatkast of andere apparaten).
Het stroomverbruik wordt gecontroleerd in de verschillende menupunten en we testen de accu en de laadadapters.
Vervolgens voeren de productie en onze service een test uit van de automatische justering & kalibratie en een test van de justering door de klant.
In de volgende stap controleren we de gegevensoverdracht naar pc-software of naar de cloud (indien beschikbaar).
Daarnaast wordt gecontroleerd of de apparaten waterdicht zijn en wordt er een valtest uitgevoerd om de behuizing te controleren op “bouwplaatsgeschiktheid”.
Documentatie, technische tekeningen, schakelschema's
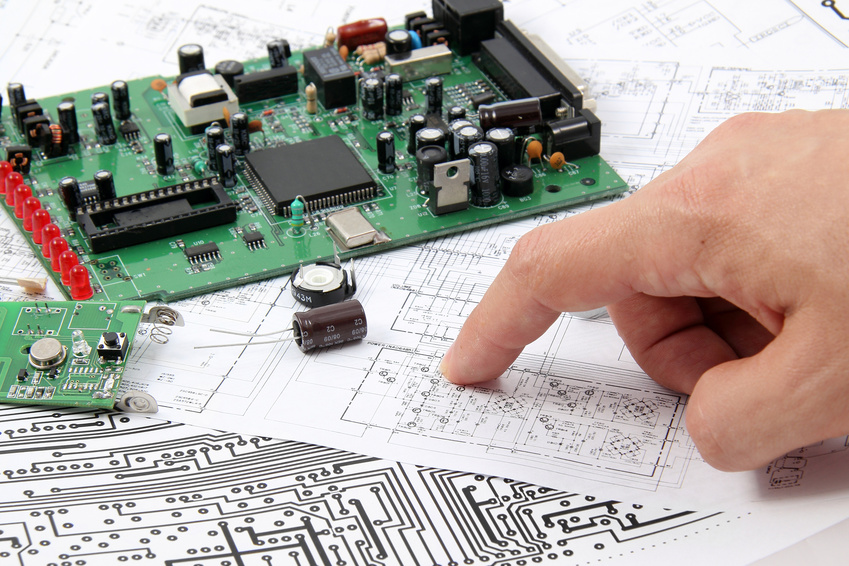
Voor het externe testcentrum worden uitgebreide documentatie, technische tekeningen, elektrische schakelschema’s en andere documenten voor het meetapparaat gemaakt.
De productieafdeling maakt de zogenaamde “nulserie” onder begeleiding van de betrokken ontwikkelaars en de benodigde documenten.
Op basis van de ervaring die is opgedaan bij het bouwen van de eerste nulserie worden “montage-instructies” opgesteld. Er wordt gedetailleerd gespecificeerd hoe een product moet worden gebouwd. Dit wordt vervolgens gecontroleerd en goedgekeurd door de ATEX-verantwoordelijke en tegelijkertijd worden QA-tests in productie geïnstalleerd.
De nulserie wordt opnieuw uitgebreid getest door QA-ontwikkeling (functionele en veiligheidsaspecten), productmanagement en verkoop (klantwensen).
Tegelijkertijd worden zogenaamde “prototypes” gemaakt en naar een extern testlaboratorium gestuurd en daar getest.
Na succesvolle externe tests wordt het certificaat van EU-typeonderzoek afgegeven door het externe testlaboratorium.
Vanaf nu moeten alle veiligheidsgerelateerde wijzigingen aan het product worden goedgekeurd door het externe testcentrum, telkens via aanvullingen op het afgegeven certificaat van EU-typeonderzoek.
Als alles naar wens is, start de serieproductie.
Bij de doorlopende serieproductie blijft het productieproces hetzelfde en wordt de kwaliteit bewaakt door QA-productie. Indien wijzigingen nodig zijn, kunnen deze alleen worden uitgevoerd na controle door de ATEX-verantwoordelijke. Hierbij wordt ook gecontroleerd of een addendum bij het certificaat van EU-typeonderzoek nodig is.
Onze kwaliteitszorg houdt niet op bij de levering van het apparaat!
Een groot aantal van de apparaten komen terug naar de fabriek voor jaarlijks onderhoud of wordt regelmatig door ons gecontroleerd tijdens de mobiele service. Bovendien registreren we elke negatieve feedback van klanten via de technische ondersteuning als een klacht in ons ERP-systeem. Dit geeft ons een zeer goede database om de kwaliteit van onze apparaten over de gehele levenscyclus van het product te kunnen beoordelen.
We weten dus vrij goed welke componenten, functies etc. na vele jaren in bedrijf nog goed werken en welke niet meer zo goed en reageren daar ook op.
Het is een lange weg van idee tot product. Maar dit is de enige manier waarop we aan de wensen van onze klanten kunnen voldoen en deze met hoge kwaliteit kunnen implementeren. We willen de processen continue blijven analyseren en verbeteren.
Vanwege het toenemende aantal producten, is afdeling ontwikkeling uitgebreid naar een team van 20 mensen.
Wij werken met veel plezier aan nieuwe oplossingen – voor u.